BUYING A HELICOPTER
Ways to anticipate and manage maintenance costs when buying a new helicopter
Often, purchase price is the lowest of all the costs you will encounter when buying a helicopter but with careful preparation you can help control what your hourly maintenance costs will run.
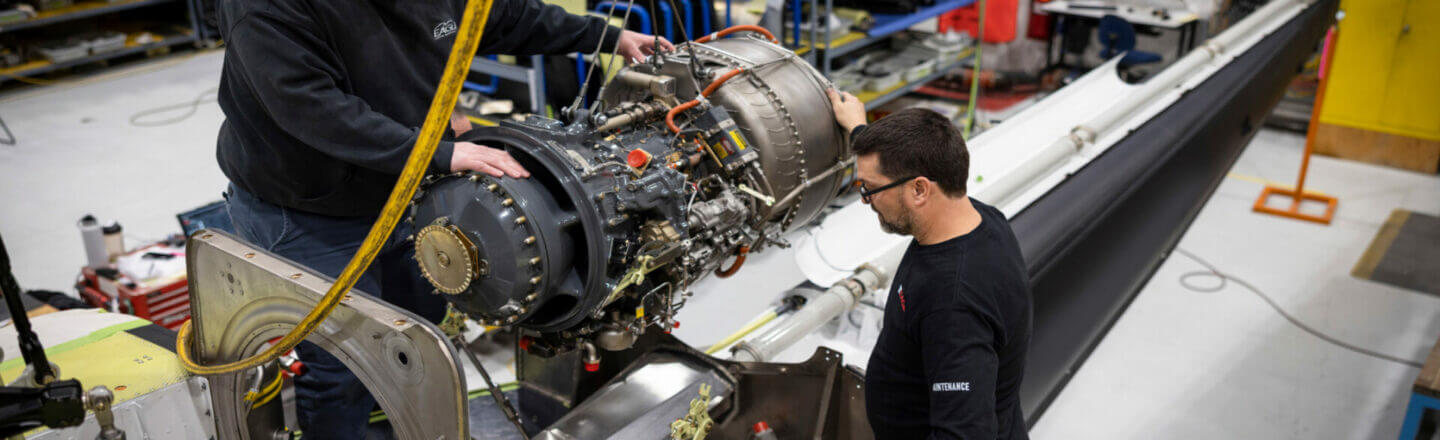
By: Jen BoyerPosted on: June 5, 2023
Often, purchase price is the lowest of all the costs you will encounter when buying a helicopter. It is not uncommon to pay far more in operating costs, which include insurance, fuel, and maintenance. While you have little control over insurance costs and no say in fuel prices, careful advanced preparation will help you control what your hourly maintenance costs will run.
Maintenance costs are often broken into several categories. Scheduled costs are those that take place predictably, such as your annual inspection and hourly inspections. These also include components that must be inspected, serviced, or replaced after a certain number of hours of use or on a specific month — the latter of which are calendar item costs. These all have a predictable component to them, but should an inspection identify an issue, additional costs will arise to repair or replace items.
On-condition/unscheduled costs are the unpredictable costs of damage and components that break. Labor is the cost per hour to perform maintenance on all of the above and parts costs are the price for all parts needed to bring the aircraft back to an airworthy condition. Labor and parts costs are often included in scheduled costs, as maintenance shops can anticipate the time it takes to perform inspections and replace parts, as well as the cost of those scheduled parts. Engine costs are often pulled out as a category of their own given their expense and specialized inspection and overhaul requirements.
Indirect costs are also important to calculate. For maintenance, this is the lost income from the aircraft being down for maintenance.
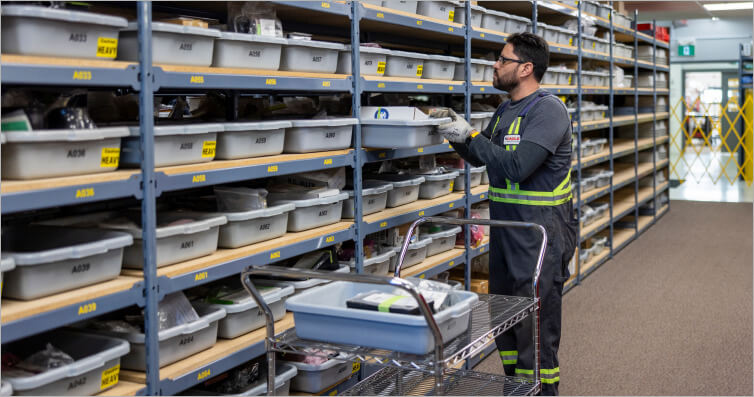
Finally, when operators and maintenance shops talk about budgeting for all of these costs, they’re often presented as hourly maintenance costs. That is, the total of all the costs above — predicted based on historical data on the aircraft make and model as well as your specific aircraft’s current hours — divided by the number of hours in a year the aircraft will fly.
It’s important to note that maintenance costs are only one piece of total direct and indirect operating costs, which include fuel, oil, insurance, hangar fees, pilot salaries, landing fees, etc.
Several resources exist to help predict overall maintenance costs and can be obtained from aircraft manufacturers, maintenance shops, and aircraft brokers.
Determining your maintenance costs
To best identify your specific maintenance costs, and help you purchase not only the right make and model but the best specific aircraft for you, you must be clear on how you will use the helicopter and how many hours a year you will fly.
“The very first question I ask anyone interested in purchasing a helicopter is ‘what is the helicopter’s mission,’” said Joe Otte, vice president and chief operating officer of FAA Part 145 repair station Thoroughbred Aviation Maintenance in Lexington, Kentucky. “Basically, you have to know how you want to use the aircraft to narrow down the make and model. Then I ask, ‘How many hours do you plan to fly in a year.’”
With that much information, Otte helps customers narrow down the right make and model for their needs. While every aircraft has scheduled maintenance items, calendar items can add up for owners operating fairly few hours a year.
“The MD 500 doesn’t have a lot of calendar life costs, so if you’re only flying 40 hours or so a year, you’re not having to add the cost of extra calendar items to your hourly maintenance costs,” Otte explained. “Bell helicopters have a lot of calendar items, and Airbus helicopters have even more. Knowing how often they’ll fly will help buyers identify a helicopter with maintenance costs that fall in their budget.”
Additionally, Otte suggests using this information to choose a specific helicopter to purchase. Helicopters with expensive maintenance coming due within 1,000 hours will cost less than those with thousands of hours left before that maintenance. A new buyer planning to fly 30 hours a year can save money upfront by choosing an aircraft with hundreds of hours before the next big time-dependent maintenance item, rather than thousands of hours. This will give the buyer years of flight, and years to save, before that big cost.
In addition to maintaining its large fleet, PHI MRO Services, a division of PHI, supports other helicopter owners and operators with a wide range of MRO services. To predict maintenance costs, PHI MRO Services uses subscription service JetNet, which helps the MRO put together a fairly accurate hourly operating cost for multiple makes and models of aircraft based on annual hours flown.
Josh Perkins, director of maintenance for PHI’s Part 145 repair station, said many larger repair shops will have similar predictive maintenance resources to help owners and operators plan for maintenance costs. According to industry numbers from JetNet, those maintenance costs can start at $280 per hour for an R22, and go up to $500+ per hour for larger aircraft like the Airbus H135, Sikorsky S-76, and Leonardo AW139.
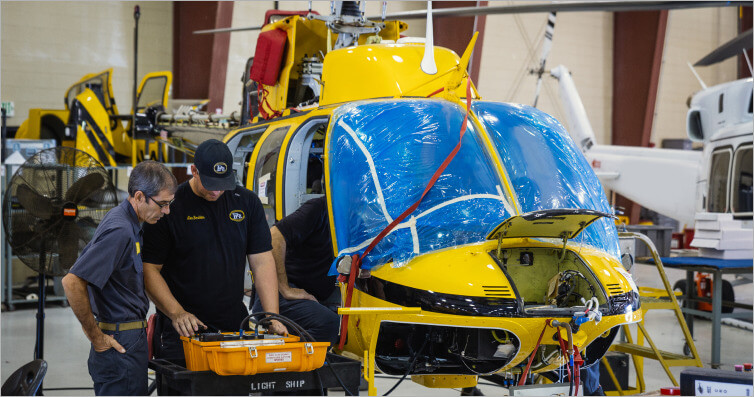
Research, research, research
Potential new owners can also reduce their maintenance costs by doing their homework in the buying process. One step is researching the support available for the aircraft make and model(s) being considered and look into programs that can support maintenance.
“There is a big difference between aircraft, but also between manufacturers and support services,” said Cory Clark, business development leader for PHI MRO Services. “How is the supply chain [and] support services outlook for that particular airframe? Additionally, looking at the supply chain and support services for the engine is key to ensuring you have access to maintenance.”
“What’s more, if you’re in an isolated area and you have a helicopter maintenance person that is, let’s say, 100 percent familiar with Airbus and you buy a Sikorsky, your local A&P or maintenance shop can provide basic support. [However,] they may not be capable of meeting the regulatory requirements around capabilities,” Perkins added. “You would then have to factor in transportation of the aircraft to a mechanic from a qualified facility.”
Perkins also recommends considering a power-by-hour (PBH) program for your aircraft’s engine, where the owner pays a monthly cost and receives parts needed for scheduled and unscheduled maintenance — often a good deal when your maintenance schedule will call for regular parts replacements. It is also beneficial in forecasting as it predicts parts needs based on hours, allowing an owner to then add in labor for a clearer hourly maintenance cost.
Prospective buyers can also save themselves extra maintenance costs by having a qualified professional they trust go through a prospective new aircraft’s logbooks to ensure all maintenance is up to date and to identify what required maintenance is coming up. If anything is missing in the logbook, despite whether the work was completed or not, it must be done again and properly logged for the aircraft to receive registration to the new owner, Perkins warned.
He also recommends looking closely at where the aircraft operated over the last several years. Salt water corrosion from operating by the ocean, damage from operating around hard sandy terrain, extreme temperatures, and the like can put considerable wear on the aircraft and are good indicators of potentially higher maintenance costs.
Also, research how often the aircraft flew or, more importantly, how long it has sat unused. A quick check of the aircraft’s tail number in FlightAware will often show its operations. If it had not experienced regular run ups or wasn’t properly prepared for storage, additional maintenance items could come up sooner rather than later, Clark said.
Factor in rising costs
Another important consideration, which can make it difficult to precisely predict long-term hourly maintenance costs, is rising costs. Parts on a whole have gone up an average of three percent a year since the pandemic began and continue to rise with raw materials shortages, noted Clark.
Related to those shortages is longer lead times for parts, especially for engines. Thoroughbred’s Otte sees piston engine work that used to take six weeks extending to closer to 18 to 24 weeks, and turbine engine work that used to take a month last up to four months, as his shop waits for parts or return of an overhauled engine due to shortages on the engine side.
Labor is also on the rise as a shortage of mechanics drives increased salaries and benefits to attract and retain qualified maintainers. “Due to inflation, labor shortages, and other cost increases, labor rates have increased as much as 50 percent in some places,” said Perkins.
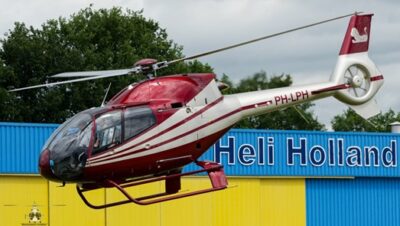
Airbus EC120B
Contact seller for price
Year: 2001
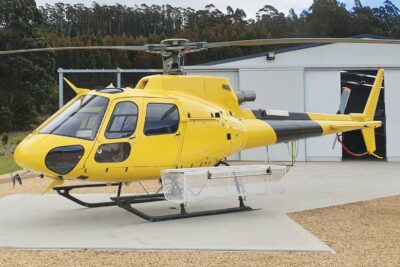
Airbus AS350B3
USD $ 1,599,000
Year: 2004
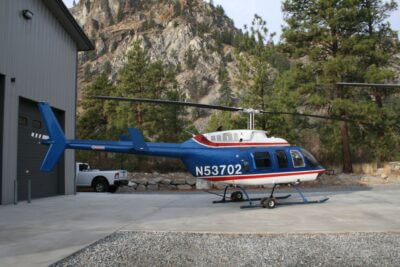
Bell 206L3
Make an offer
Year: 1992
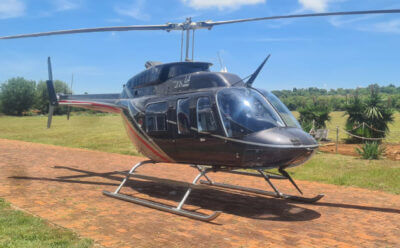
Bell 206L4
Make an offer
Year: 1996
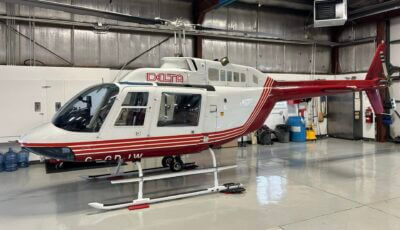
Bell 206B3
Contact seller for price
Year: 1979
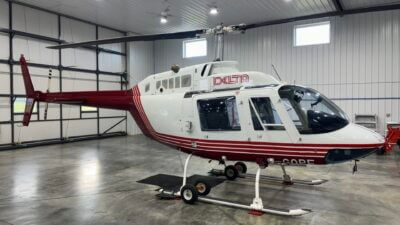
Bell 206B3
Contact seller for price
Year: 1980
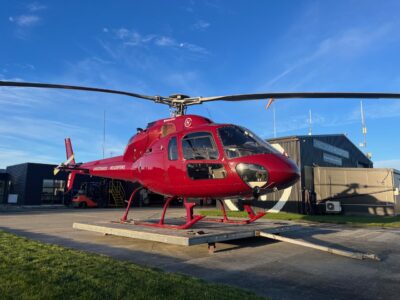
Airbus AS355F2
Contact seller for price
Year: 1992
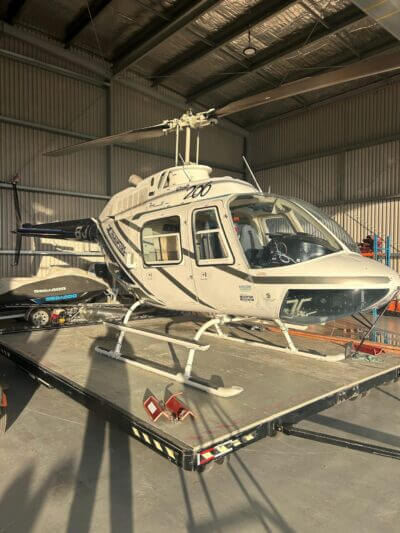
Bell 206B3
Contact seller for price
Year: 1973
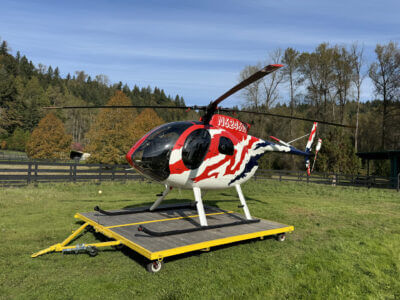
MD Helicopters 369A
Contact seller for price
Year: 1968
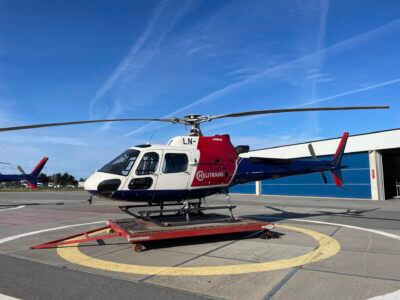
Airbus H125
EUR € 2,400,000
Year: 2020